Porosity in Welding: Identifying Common Issues and Implementing Finest Practices for Prevention
Porosity in welding is a prevalent issue that frequently goes unnoticed up until it triggers considerable troubles with the honesty of welds. In this conversation, we will certainly discover the vital factors contributing to porosity formation, analyze its detrimental impacts on weld efficiency, and go over the best techniques that can be adopted to lessen porosity event in welding processes.
Typical Sources Of Porosity

Using filthy or wet filler materials can introduce pollutants into the weld, contributing to porosity problems. To alleviate these usual reasons of porosity, thorough cleaning of base metals, proper securing gas option, and adherence to optimum welding criteria are essential practices in attaining premium, porosity-free welds.
Effect of Porosity on Weld High Quality

The existence of porosity in welding can substantially jeopardize the structural integrity and mechanical homes of welded joints. Porosity creates gaps within the weld steel, damaging its total stamina and load-bearing capacity. These gaps work as anxiety concentration factors, making the weld extra prone to breaking and failing under used tons. Additionally, porosity can lower the weld's resistance to deterioration and other ecological aspects, even more diminishing its long life and performance.
One of the main consequences of porosity is a reduction in the weld's ductility and toughness. Welds with high porosity degrees tend to exhibit reduced influence strength and lowered capability to flaw plastically before fracturing. This can be specifically worrying in applications where the welded elements are subjected to vibrant or cyclic loading problems. Furthermore, porosity can hamper the weld's capacity to efficiently send forces, resulting in early weld failing and potential safety dangers in critical structures.
Finest Practices for Porosity Prevention
To enhance the structural integrity and quality of bonded joints, what details actions can be implemented to minimize the occurrence of porosity throughout the welding procedure? Porosity prevention in welding is important to guarantee the Web Site integrity and strength of the last weld. One efficient method appertains cleaning of the base metal, getting rid of any kind of pollutants such as rust, oil, paint, or dampness that can result in gas entrapment. Guaranteeing that the welding equipment remains in great problem, with clean consumables and appropriate gas circulation rates, can also significantly lower porosity. Furthermore, maintaining a secure arc and managing the welding parameters, such as voltage, existing, and take a trip rate, assists develop a regular weld pool that minimizes more the danger of gas entrapment. Making use of the appropriate welding technique for the particular product being welded, such as adjusting the welding angle and weapon position, can even more prevent porosity. Regular evaluation of welds and prompt removal of any kind of concerns determined during the welding process are crucial techniques to stop porosity and produce high-quality welds.
Value of Correct Welding Techniques
Implementing appropriate welding techniques is paramount in ensuring the structural stability and high quality of welded joints, developing upon the foundation of effective porosity prevention steps. Extreme warm can lead to boosted porosity due to the entrapment of gases in the weld pool. Furthermore, using the appropriate welding parameters, such as voltage, current, and take a trip rate, is essential for achieving audio welds with very little porosity.
Additionally, the choice of welding procedure, whether it be MIG, TIG, or stick welding, must align with the specific needs of the job to guarantee ideal outcomes. Appropriate cleansing and preparation of the base steel, in addition to picking his comment is here the ideal filler material, are additionally necessary components of skillful welding methods. By sticking to these best methods, welders can minimize the danger of porosity development and produce high-grade, structurally sound welds.
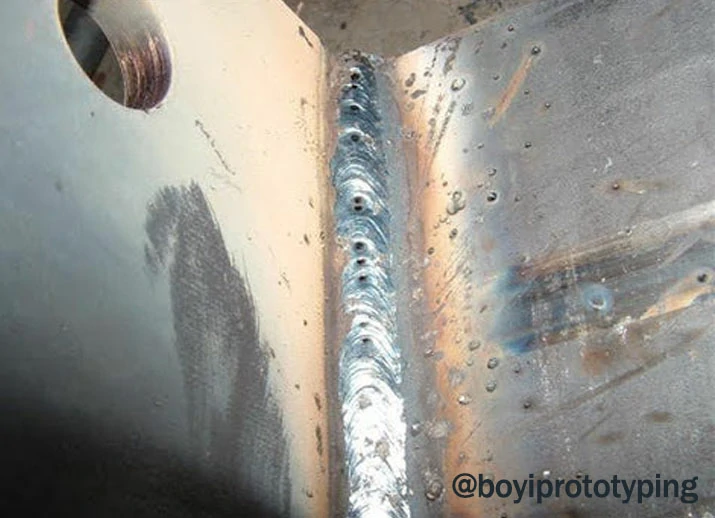
Examining and Top Quality Control Measures
Quality assurance steps play an important duty in validating the integrity and dependability of bonded joints. Testing procedures are vital to identify and protect against porosity in welding, making sure the toughness and sturdiness of the end product. Non-destructive screening methods such as ultrasonic testing, radiographic testing, and visual inspection are generally used to determine prospective problems like porosity. These strategies enable the evaluation of weld quality without jeopardizing the integrity of the joint. What is Porosity.
Performing pre-weld and post-weld evaluations is additionally crucial in keeping quality control standards. Pre-weld inspections include confirming the products, equipment setups, and tidiness of the workplace to avoid contamination. Post-weld examinations, on the other hand, evaluate the last weld for any kind of issues, consisting of porosity, and confirm that it meets defined standards. Carrying out a comprehensive high quality control plan that includes extensive testing procedures and inspections is paramount to decreasing porosity problems and guaranteeing the overall quality of bonded joints.
Conclusion
In conclusion, porosity in welding can be an usual issue that influences the quality of welds. By determining the common sources of porosity and applying finest practices for prevention, such as proper welding techniques and screening steps, welders can guarantee premium quality and trusted welds. It is vital to prioritize prevention approaches to reduce the occurrence of porosity and preserve the integrity of bonded frameworks.